Press
Factory rebuild complete
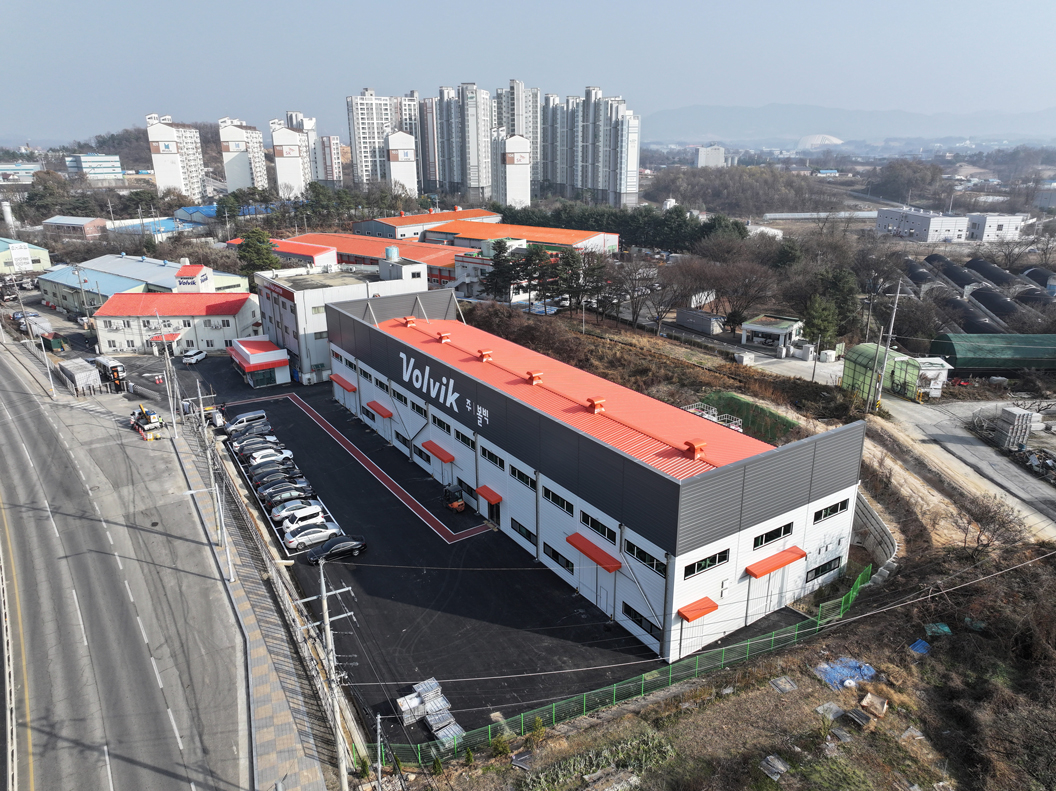
- Transforming into an eco-friendly smart factory by adopting electric heating method
- Korea's only high-tech 'R&D center' prepares for a global leap forward
South Korean golf brand Volvik (CEO Hong Seung-seok) has rebuilt its first factory and started mass production to become a global brand.
In November of last year, a fire destroyed Volvik's first factory in Eumseong-gun, Chungcheongbuk-do. Despite facing adverse circumstances, Volvik used this as an opportunity to rise to the occasion and renewed the aging existing facility with state-of-the-art equipment. After more than a year of preparation, the company completed the reconstruction of Factory 1 and built a state-of-the-art golf ball production plant on a total area of 14,876 square meters, including Factory 2, which was completed in 2019.
With this, Volvik now has a world-class production capacity of 4 million dozen balls per year. Two million dozen will be produced in-house at the Eumseong 1 and 2 factories, and another two million will be outsourced, for a total of four million dozen. This is an increase of 1 million dozen per year compared to before.
Factory 1 produces 'Core'. The process of thermoforming cores with excellent rebound elasticity using synthetic rubber is the core and role of Factory 1. It has become the world's largest specialized dual-core production factory. The core of Volvik's products, dual-core is a technology that makes the "inner core" harder and the "outer core" softer. The reconstruction has improved the process, resulting in higher quality 3- and 4-piece premium balls that can be supplied in large quantities.
The thermoforming press was also converted from a conventional heat-and-cool boiler system using diesel and LNG gas to an electric heating system, laying the foundation for an eco-friendly smart factory. The electric heating method enabled carbon reduction and improved the working environment for workers.
In addition, by applying a cooling method that quickly controls the temperature of the thermoforming press, product productivity increased by more than 30%, and the structure of the press was improved and automated to increase the unit productivity of the thermoforming press, resulting in an innovation that reduced the manpower and time required for production by more than 40%.
Plant 2, which was completed with automation in 2019, is responsible for dimple covering the cores and mantles produced in Plant 1 and producing finished products through glossy/matte coating, printing and packaging processes. Volvik has completed state-of-the-art automation at both plants, making them state-of-the-art factories that maximize production efficiency and quality excellence.
The company also has a world-class HIGH TECHNOLOGY R&D research facility. The R&D laboratory is staffed with researchers and engineers specializing in golf data analysis, and is the first golf equipment company in Korea to have a 400-meter-long test field in Pyeongtaek, a performance test robot, and analytical equipment that can track the trajectory of a golf ball and data the performance of the ball.
"With the reconstruction of Factory 1, Volvik has reached a new turning point as a KICONIC GOLF BRAND representing Korea, and we will move forward as a true golf brand that is recognized for its excellent performance and quality not only in Korea but also overseas," said a Volvik official.